December 7, 2022
7 min read
Optimizing manufacturing excellence: 5 strategies for improving tooling resources
.png)
In the ever-changing realm of modern manufacturing, embracing innovation has become the cornerstone of sustainable success. A paradigm shift is underway that challenges manufacturers-whether moldmakers, molders or OEMs-to rethink their strategies. Instead of focusing on data collection, the focus has shifted to leveraging readily available data to gain analytical insights that can improve efficiency. The current landscape of tight schedules, increasing demands, supply chain complexity, resource constraints, and remote operations underscores the critical role of efficiency and performance optimization.
The process begins with identifying specific needs. Whether the goal is to manage, monitor, maintain, or maximize mold performance, mold makers, molders, and OEMs have tailored solutions available. These solutions fit different budgets, timelines, and resource constraints, offering distinct levels of visibility aligned to individual business needs.
Leveraging the proactive use of data
The mold is the flagship of a printer's or OEM's inventory, making it imperative to proactively understand its inner workings. The imperative is to shift from a reactive to a proactive attitude, as real-time diagnostics could prevent unforeseen problems. Consider the scenario in which cycle times or downtime gradually increase. Is it not wiser to anticipate these trends rather than face the repercussions of an unexpected setback? The prevention of unplanned mold stoppages assumes paramount importance in the quest to maximize productivity.
The concept of "smart mold" is at the heart of this research. In an age when intelligence pervades all aspects of manufacturing, it follows that molds should evolve as well. The integration of self-diagnostic capabilities within molds, facilitated by cutting-edge technology, can revolutionize performance monitoring. Such molds can continuously transmit critical data, enabling proactive observation of trends, or trigger alerts via sensors when critical failures or deviations from tolerances occur.
Extracting value through the supply chain
Mold data, a treasure trove of information, has distinct value for each link in the production chain. OEMs recognize the need for data for maintenance and proper asset utilization. Mold makers need this data for optimal production of quality parts and to promote continuous improvement initiatives. Moldmakers are looking for information to refine their products and recommend preventive maintenance strategies.
The Transition
The transition to smarter mold utilization is not uniform; customized "smart" technologies offer different paths for mold makers, moldmakers, and OEMs. To embark on this transformational journey, an electronic monitor serves as a bridge.
An OEM can specify electronic monitoring during the mold purchase, and then get to real-time monitoring at the moldmaker's site.
Moldmakers can use electronic monitors to improve service offerings to OEM customers while simultaneously collecting crucial data on the mold.
Moldmakers can benefit from integrating electronic monitors into tool specifications, simplifying documentation requests and increasing visibility into mold maintenance.
Five approaches to improve mold asset management
1. Asset (QR) labels: Use QR code-based asset management for tracking, file sharing, and archiving vital documents such as PM logs, mold drawings, and BOMs.
2. Mold monitoring: Improve asset management and performance analysis through mold monitoring. This system provides information on cycle time, efficiency, OEE, and local file sharing. Its reports enable mold makers, moldmakers, and OEMs to speak a shared language.
3. Remote Validation: Facilitate remote mold validation using portable real-time monitoring systems. This cost-effective approach provides crucial data, accelerates validation, and optimizes resource allocation.
4. Comprehensive real-time monitoring: Provides a comprehensive view of molding operations globally, improving transparency and asset management through real-time and historical data. Customizable visibility settings address specific needs.
5. System cooling optimization: Prioritize cooling optimization, as cooling is a significant part of cycle time. Monitoring water flow, temperature and pressure in molds can produce significant gains in profitability.
Strategic roadmap to excellence
The quest for quality parts that are reliable and delivered on time, fostering a favorable ROI, unites moldmakers, molders, and OEMs. The decision to embark on this journey is no longer a matter of "if," but rather "where" to begin the transformation to data-driven efficiency. The optimal path involves setting well-defined end goals and meticulously mapped out step-by-step plans. By committing to leveraging smart data, manufacturers can increase operational efficiency and defeat non-value-added costs, ensuring their longevity in an ever-changing manufacturing landscape.
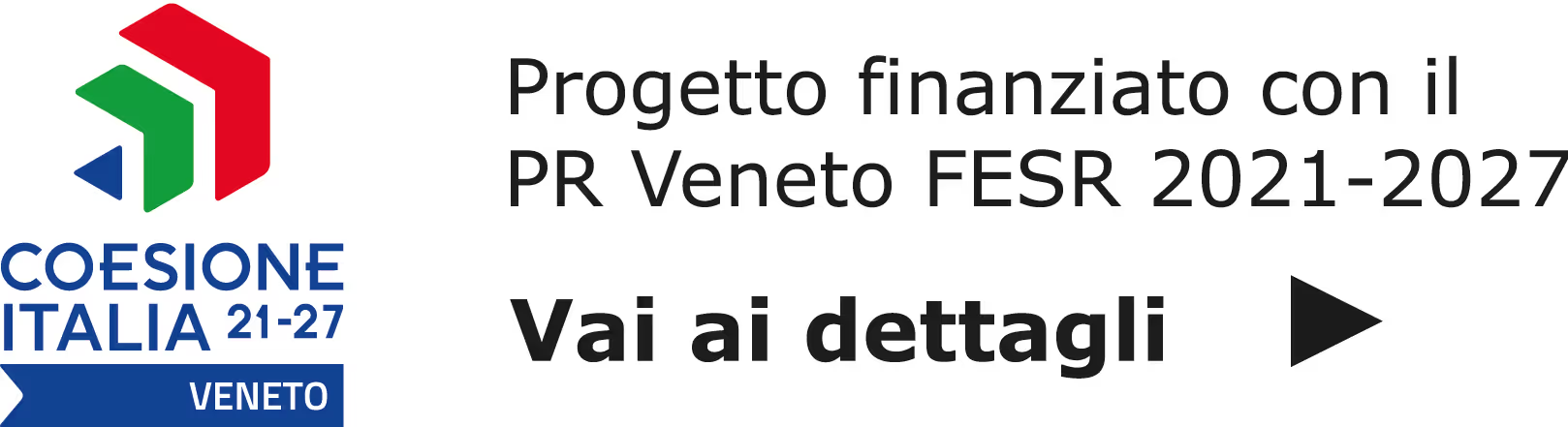
You might also like
MAXIMIZE OEE
Your Tools, Our Technology
Take control of your industrial tools' performance. Our demo will show you how to leverage real-time data, predictive analytics, and comprehensive asset management to minimize downtime and maximize productivity.
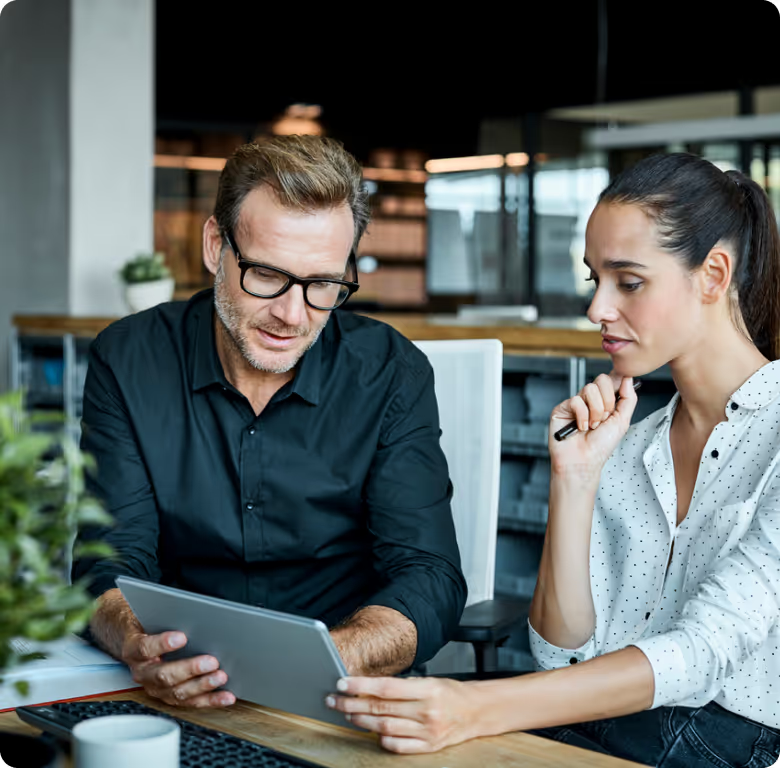
“New eyes on your molds production to lead performance towards operational excellence.”
Emanuele Quarin, Digital industrial operations director