.png)
How an international company increased by 2% the OEE
They managed to gain maximum control of their molds and supply chain data
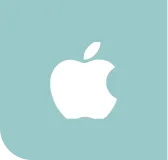
The client is an international company in the household appliances sector, with a large fleet of molds located between in-house production and outsourced production at third party suppliers.
The inconsistency of the in-house data, where the accounting of the molds was kept manually, and the impossibility of collecting data from the assets granted on loan to suppliers, were posing numerous challenges in the mold management.
Client needs
Saturation and performance. Among the most pressing problems there was the difficulty of measuring mold saturation and performance, both in-house and at suppliers. This resulted in wastes in terms of energy costs, man-hours, and unnecessary asset duplication.
Maintenance. There was also a substantial difficulty in planning maintenance in a preventive manner and in verifying the maintenance carried out by suppliers. Both aspects increased the risk of compromising the health of the asset, thus making more frequent the recourse to extraordinary maintenance (at the expense of the client).
Supplier monitoring. The poor visibility into the outsourced production did not allow anticipating any delays in parts deliveries, significantly increasing the risk of stock-outs and consequent production downtimes. Furthermore, the difficulty in acquiring and exchanging information did not favor collaboration between the client and the suppliers for the timely resolution of problems.
Inventory. Given the number of molds located around the world, it was difficult to have a single database for molds with consistent data, making it necessary to hire auditors responsible for asset inventory.
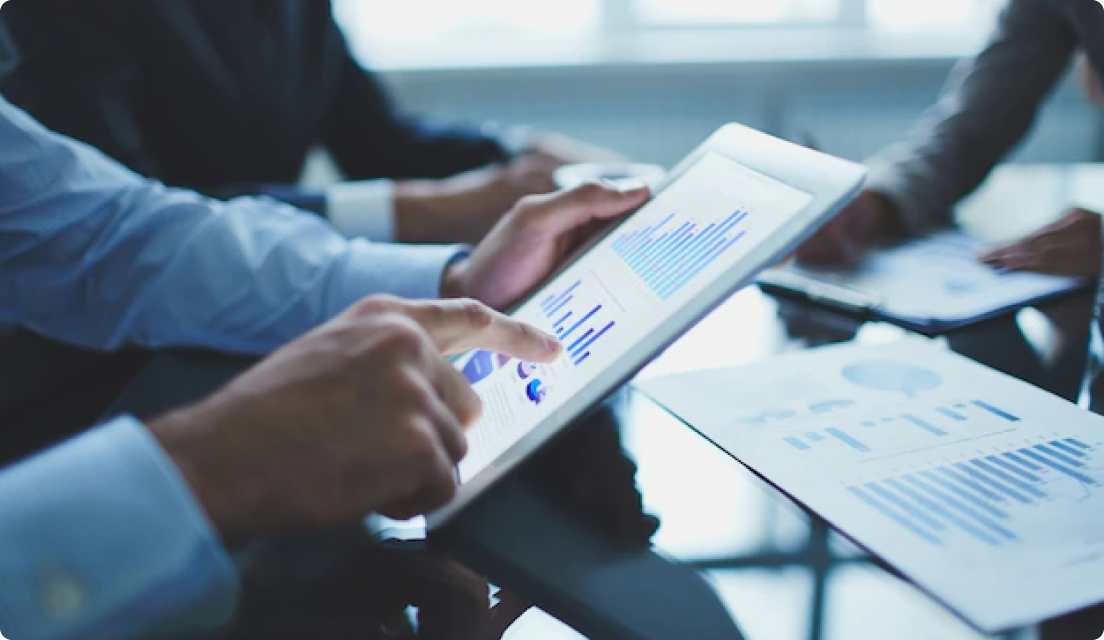
Solution benefits
Maximization of mold performance and saturation. Through our platform it was possible to monitor the saturation and performance of each mold, thus identifying underused and/or under-performing assets. The insights generated by our solution have been fundamental in optimizing CAPEX on new molds and increasing tooling OEE, as well as reducing overtime work by 10%. Furthermore, it was possible to carry out corrective actions to address declines in asset performance.
Maintenance optimization and verification. The integration of the cycle count data into the CMMS of the reference production plants has enabled preventive maintenance based on the actual use of the asset. Furthermore, thanks to MATIX it was possible to verify the maintenance carried out by the suppliers, with a 10% reduction in costs related to extraordinary maintenances charged to the client.
Supply chain visibility. Thanks to MATIX it was possible to monitor the progress of production at the most strategic suppliers. In this way, the client was able to reduce the risks associated with stock-out by implementing preventive activities. Furthermore, by highlighting deviations from the standard process parameters, our system has made it possible to request corrective maintenance from suppliers in a timely manner, resulting in a reduction in the scrap rate and in a longer lifespan of the mold.
In all these cases MATIX enabled transparency in the supply relationship to the benefit of both parties, for example by allowing an objective verification of the extra-costs that the customer had to pay to the suppliers. Finally, both the customer and the suppliers appreciated the speed and ease of installation of the solution.
Automated inventory. Thanks to MATIX it was possible to provide the customer with the location of the assets over time, following their movements without interruptions in monitoring thanks to cellular connectivity. Through consistent mold data, aggregated performance KPIs and complete maintenance history, MATIX has made it possible to collect all the business-relevant data related to the molds in a single system, reducing asset management and auditing activities by 50%.
Results
-10% Extraordinary maintenances
+2% OEE
-10% overtime labour
-50% Mold Management activities
-5% CAPEX for new molds
More resilient supply chain
You might also like
MAXIMIZE OEE
Your Tools, Our Technology
Take control of your industrial tools' performance. Our demo will show you how to leverage real-time data, predictive analytics, and comprehensive asset management to minimize downtime and maximize productivity.
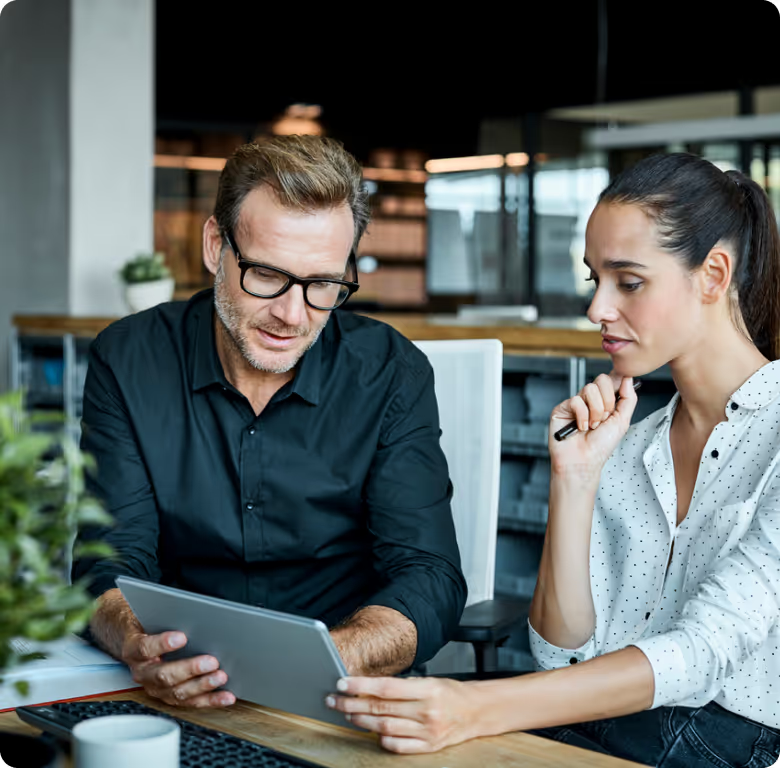
“New eyes on your molds production to lead performance towards operational excellence.”
Emanuele Quarin, Digital industrial operations director